2024 in Review
Fellow Shareholders
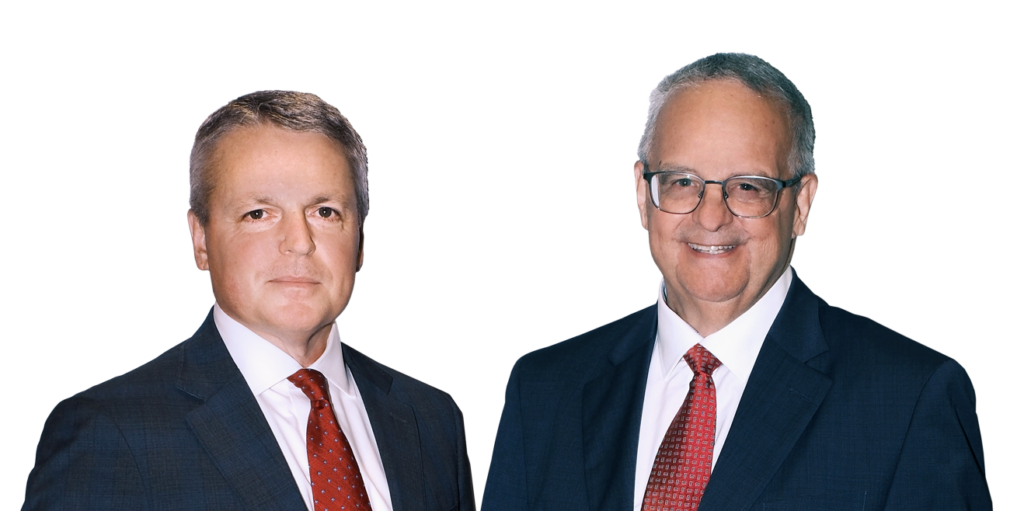
In 2024, Toromont generated revenue of just over $5 billion, 9% higher than in 2023, earned $506.5 million or $6.18 basic per share, a 4% year-over-year reduction, and delivered Return on Shareholders’ Equity of 19.2%.
After several years characterized by unique market dynamics, and in the context of opportunities and challenges in 2024, this was a solid outcome.
While annual results are important, more telling is performance through market cycles. Delivering value on this long-term basis is a key objective for our Board and management team. This mindset drives our capital allocation decisions, our duty of care for our Toromont team members and the enduring partnerships we seek to build with customers and world-leading OEMs. Decades ago, this mindset inspired our economic model of delivering specialized capital equipment paired with product support across diversified vertical markets while maintaining a strong financial position that further mitigates cyclical risk.
Scrutinizing Toromont on a full-cycle basis demonstrates the value of this approach. Over the past five years, we invested over $1.1 billion in our rental fleets and capital infrastructure, including a business acquisition, giving us a better and broader platform to serve customers and represent our partners. For our workforce, we provided more than 142,000 hours of skills training to empower employees. For shareholders, 5-year average annual revenue growth of 7.1% translated into 5-year average annual growth in EPS of 13.4%, an ROE average of 20.3% and five consecutive annual increases in Toromont’s dividend. (In February 2025, our Board of Directors increased the dividend for the 36th consecutive year.) While deploying the balance sheet, strong cashflows allowed Toromont to reduce net debt to total capitalization to -9% (net cash position) from 15% at year-end 2019.
We are proud of this performance, delivered as it was during an economic cycle that began with a global pandemic, included supply chain constraints, significant increases in inflation and interest rates, and ended in 2024 with a transition in those externalities. Supply chains have now largely normalized and other factors such as interest rates have trended lower, supporting new product and service investments by our customers in 2025. At the same time, we are determined to build on Toromont’s success not just this year but throughout the next business cycle.
Financial highlights
FY ’24 | FY ’23 | FY ’22 | |
---|---|---|---|
Revenues* | $5.0B | $4.6B | $4.1B |
Net Earnings* | $507M | $529M | $450M |
Basic EPS* | $6.18 | $6.43 | $5.47 |
ROCE | 25.7% | 30.4% | 32.3% |
Net Debt / Total Cap | -9% | -17% | -14% |
*Continuing operations basis |
Consecutive dividend increases for 36 years
Toromont has paid dividends every year since 1968 including 2024 when our dividend was $1.92 per share. In 2025, our Board increased the dividend for the 36th consecutive year to an annualized rate of $2.08 per share.
Connect26, Toromont’s three-year plan
To guide our long-term ambitions, Toromont creates three-year plans. In 2024, we introduced Connect26, our new growth and improvement roadmap. It is anchored by our north-star aim of delivering 18% ROE over the business cycle and is faithful to our core strategies of expanding markets, broadening product offerings, investing in resources, strengthening product support and maintaining a strong financial position.
To support those objectives, Connect26 commits us to building new and stronger connections with customers, employees, partners and communities and leveraging the connections that exist between Toromont businesses for synergistic advantage. Below we describe actions we are taking and disciplined investments we are making to win business today and create value for tomorrow.
Connecting to the rental market in new ways
Toromont serves a large rental equipment market through Toromont Cat, Toromont Power Systems, Battlefield Equipment Rentals – The Cat Rental Store (Battlefield), Jobsite Industrial Rental Services (Jobsite), SITECH Eastern Canada (SITECH) and Toromont Material Handling. To improve our long-term positions, we made several moves in year one of Connect26.
Informed by marketplace studies, Battlefield opened two locations in Ontario (Pembrook and St. Thomas) and offered customers a better experience by expanding its Sainte-Madeleine, Québec store and moving into a new facility in Sherbrooke. While storefront investments are important and Battlefield now operates in 70 locations across Eastern Canada, back shops continue to focus on getting rental equipment in a return-to-ready state quickly after customer use to drive better utilization. Recognizing that customers connect with Battlefield for leading brands, we introduced trench safety products into our Ontario network with good uptake.
To build long-term connections to Western Canadian industrial rental markets, Jobsite opened a branch inside Battlefield’s Winnipeg store. Jobsite now has facilities there as well as in Edmonton, Fort McMurray, and Burnaby (all opened in 2023) in addition to 10 locations in Eastern Canada. While a start-up presence requires patient capital, Jobsite successfully secured several customer projects in its new territories, including the provision of tool cribs used during the maintenance shutdown of a west coast refinery.
We also changed how we go to market with Compact Construction Equipment (CCE) products. Responsibility for sales of these machines was transferred to Toromont Cat from Battlefield with two advantages: Battlefield returns to its roots as a rental company first and foremost; and, Toromont Cat customers now have the same connection point to buy all Caterpillar machines we represent, large and small. We look to build on this shift by selectively introducing CCE retail showrooms, leveraging the capabilities of the CCE sales force as part of Toromont Cat, and continuing to drive the CCE rental opportunity from Battlefield. To open 2025, Battlefield assumed responsibility for the pump rental business previously managed by Toromont Power Systems. Construction site dewatering systems are an ideal complement to Battlefield’s rental product portfolio.
Toromont Material Handling (TMH) used year one of Connect26 to expand its rental fleet across all equipment categories to better serve customers – including those whose business volumes periodically surge and those who prefer long-term, lease-style arrangements. To improve financial and time utilization, we will leverage core rental business disciplines at TMH starting in 2025.
While organic growth remains our priority, Toromont completed the acquisition of Tri-City Equipment Rentals in the third quarter. Located in southwestern Ontario, this business specializes in renting heavy equipment. Although this acquisition did not make a material difference to revenues, it connected us to new customers and insights we will leverage in managing a dealership-wide fleet of ~600 heavy rent machines and attachments.
Connecting customers to the circular economy with new capacity
Rebuilding engines, transmissions, drive trains, suspension groups and hydraulic cylinders is one of the ways Toromont connects customers to the environmental and cost advantages of the circular economy. To serve the needs of customers for decades to come, including those whose machines use hybrid drivetrain and battery electric technologies, we built – and in May 2024 – occupied a 143,000 square foot Toromont Remanufacturing (TR) Centre in Bradford, Ontario. That marked the start of a months’ long process to commission and optimize the plant’s sophisticated equipment including automated soda blasting (for component cleaning) and engine dynamometers that arrived before year end.
While 2024 was a staging year, the team in Bradford began to capitalize on the plant’s footprint and features. Rebuilding generators for urgent reuse by customers in Iqaluit, including 26-tonne Cat® C280s, demonstrated the value of extra facility floor and yard space and overhead crane capacity that makes large-scale work more efficient. This assignment also underscored the synergistic connections that we leverage between TR and other parts of our business. In this case, Toromont Power Systems sourced the used generator sets, managed a complex set of northern Canadian delivery logistics and commissioned the rebuilt models in Iqaluit.
To bring the new Centre up to nameplate capacity in 2025, plant management is making a concerted effort to recruit additional technicians through open houses with the added benefit of building community connections and a public profile for Toromont in the Bradford region.
Through this dedicated facility and four others in Eastern Canada, Toromont is well connected to customers in power, mining, transportation and construction for whom our component exchange program serves as a vital backstop for business continuity. The exchange program is the subject of ongoing inventory investments informed by telematics monitoring of machine hours of use compared to predicted wear cycles.
In 2025, all of our remanufacturing operations in Eastern Canada will roll out a made-at-Toromont production planning system that will support technician training and scheduling, standardize workflow for greater efficiency and repeatability, and when linked to the Toromont Hub portal, improve the customer experience.
In 2026, we plan to start construction of a new TR centre on owned land adjacent to our existing site in Québec City. This new 76,000 sq.ft. facility will position Toromont to efficiently and effectively serve in-region customers, complementing our other TR locations in Pointe-Claire, Québec, and Thunder Bay, Bradford and Concord, Ontario. Located on owned land beside our existing branch, estimated construction costs are approximately $20 million, subject to site plans and permits.
Connecting with customers by offering them the right connection points
From tire-kicking to machine disposition, we strive to give customers easy access to Toromont’s broad portfolio of products and services. Our connections often begin by evaluating the customer’s objectives for productivity, utilization and lifetime cost of ownership. In fleet situations, this may result in the customer purchasing new Caterpillar equipment for key high-utilization applications; engaging SITECH for professional site positioning support services; acquiring low-hour Cat used equipment for secondary applications; supplementing fleets through our heavy rent division and Battlefield; and divesting certain machines and attachments through our dealerships or the Toromont Equip online marketplace at a time that optimizes resale value.
Taking a holistic approach to serving customers is a key objective, which is assisted by continuous investments in employee training, easy to navigate but comprehensive e-commerce sites, a variety of digital tools and inter-company teamwork. We are also investigating how artificial intelligence can add speed and efficiency to our efforts.
Ensuring the voice of the customer is always heard and heeded is crucial to our planning efforts. In 2024, Toromont Cat surveyed a cross-section of customers who own between one and 15 machines. The findings told us that for these customers, our parts counter teams are their most valuable connection point. To address this insight, we organized soft skills training for the members of our parts and sales teams who have been with us for less than five years – a cohort that includes those who missed out on in-person classroom work during the pandemic.
Connecting all customers to lifecycle product support
Placing equipment in the field is a key part of our business model. In 2024, we had some notable successes including the delivery of over 270 mining machines in our territories as well as several large construction equipment fleets in various parts of Eastern Canada. Commissioning new equipment like Cat® 798 mining trucks with payloads exceeding 400 tonnes and next-generation hydraulic mining shovels is a big task, but supporting customers as they use them is an even bigger job, lasts far longer and for shareholder value creation, adds some revenue stability and growth potential during low periods in the capital equipment purchasing cycles in our various markets.
Toromont has long provided product support in various forms – from comprehensive multi-year Customer Value Agreements (CVAs) through to simple parts kits for do-it-myself (DIM) customers. Focused efforts to grow and renew point-of-sale CVAs for both new and used equipment are important aspects for our customer value proposition and this focus adds efficiency to CVA administration and operations. To address demand now and in the future, Connect26 saw us expand our parts warehouse in Timmins and our shop in Sudbury (which supports service for the first fleet of Cat® Command 793F autonomous haul trucks operating in our territories) and set up a remote camp to serve Atlantic Canada’s largest open pit gold mine. More investments are planned in 2025, including in a general parts distribution centre near Toronto, to ensure we remain connected with the product support opportunity and lead our industry with on-time parts fulfilment. Additionally, we plan to construct Toromont Cat’s newest branch. This 48,000 sq.ft. facility in Brooklin, Ontario will support customers in south-central Ontario when it is operational in the second half of 2026. Land acquisition and construction costs are estimated at $35 million, subject to final site plans and permits.
Connecting to long-term and emerging opportunities
Like previous Toromont plans, Connect26 focuses on winning business and delivering results every year, but always with the long term in mind. It commits us to preparing for trends that will shape our world five to 10 years (and more) from now. Electrification, the transition to alternative fuels, the development of microgrids, battery storage, energy transfer systems and small modular reactors, machine automation, as well as data centre scaling to meet the rising demands of artificial intelligence, are areas to watch. Caterpillar, our largest OEM partner and a global technology leader, dedicates significant resources to addressing key trends and Toromont will benefit from these efforts.
However, our businesses must also contribute by ensuring we have the right skills, services and resources to assist customers. With that in mind, in February 2025, we announced a strategic investment in AVL Manufacturing (AVL), a leader in designing and fabricating power generation and storage enclosures. These specialized enclosures are used in the rapidly growing data centre market in eastern North America and are often integrated along with standby and prime power packages produced by Caterpillar dealers, including Toromont Power Systems. By taking a 60% ownership position in AVL, we secure our own supply, gain access to a platform to expand our market to other regions and benefit from the complementary capabilities of the AVL team in Hamilton, Ontario led by Vince DiCristofaro, AVL’s President.
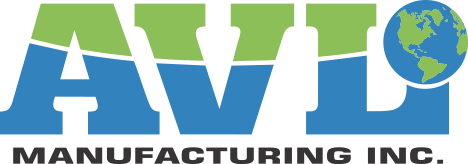
We have assigned Toromont Cat’s Chief Operating Officer to oversee our data centre opportunity as well as the aforementioned expansion of our TR capabilities and integration of Tri-City Equipment Rentals.
AVL is not the only manufacturing company in the Toromont portfolio. Through years of innovation, CIMCO has enabled ice rink and industrial customers to switch to natural CO2 and ammonia refrigerants in place of environmentally harmful fluorinated gases, optimize energy consumption through heat recovered during the process of cooling, and harness clean power. With these capabilities, CIMCO is pursuing several long-term growth avenues. One is to further penetrate the U.S. market which accounted for 24% of CIMCO’s revenue in 2024. U.S. customer interest in natural refrigerants is growing and the 2024 purchase of CIMCO CO2 packages by the NHL’s Philadelphia Flyers added to our market profile. The NHL also endorsed CIMCO’s iQ Vision, a new system that captures precise ice rink temperature data from thermal imaging and advanced sensors to enable automated quality control monitoring and in-game reporting. To connect more cost-effectively to U.S. markets, CIMCO opened a prefabrication facility in South Carolina in 2023.
In Canada, CIMCO’s recently formed thermal decarbonization team is building connections with dozens of municipalities to help them identify ways to achieve 2030 and 2050 GHG reduction goals. These year-long studies enhance participants’ knowledge of how to achieve net-zero objectives and have so far resulted in three new capital project wins for CIMCO. District heating and cooling is another emerging market well suited to CIMCO’s capabilities. In 2024, CIMCO successfully completed the initial phase of its first heat pump systems’ installation now in use by the community of Blatchford, Alberta. The sales cycle for thermal management innovations requires patience and is assisted by awareness generated by events such as CIMCO’s 2024 Innovation Summit in Edmonton. It was attended by ~140 customers and multiple industry influencers.
Connecting with our exceptional people and a high-performance culture
Toromont is driven to perform by an exceptional workforce of ~7,300 people across Canada and in the United States. We do not take their capabilities and contributions for granted. Under the auspices of Connect26, we will continue to invest to build a great employee experience, rooted in Toromont’s corporate values and our belief in the power of engagement. Our decentralized decision-making structure provides the right environment for personal growth, professional development and engagement at all levels. We believe that investing in our workforce and cultivating a high-performance culture where safety is paramount ultimately leads to positive outcomes for our customers and shareholders. We thank the people of Toromont for their hard work in 2024.
Toromont is driven by an exceptional workforce of ~7,300 people across Canada and the United States.
Connecting with wise counsel
Toromont’s Board of Directors plays an active oversight role in all aspects of the company using a proven governance framework more fully described in our Management Information Circular. While the framework is important, it is the skills, knowledge, experience and integrity of the people who serve as Directors that are the most fundamental determinants of effective governance.
For the past 13 years, our Board and our company have benefitted from the presence of Jeffrey S. Chisholm who retires in 2025. Mr. Chisholm served as Vice Chairman of the Board, the Chair of our Human Resources and Health and Safety Committee, on our ESG Committee and, in his early years, on the Audit Committee. In every role, he demonstrated the essential qualities that every shareholder would want in a corporate director: independence, a willingness to challenge management, while providing deep business insights and a passion for continuous improvement. We thank Jeff for his leadership and
wise counsel.
In preparation for this change, and to ensure our Board remains well positioned to add value, we welcomed Ave Lethbridge and Paramita Das as Directors. Ms. Lethbridge has 30+ years’ experience in the energy industry, most recently as Executive Vice President and Chief Human Resources and Safety Officer at Toronto Hydro. Ms. Das has 20+ years’ experience in the resources, mining and materials industry, including almost a decade with Rio Tinto, most recently as Global Head of Marketing, Development and ESG (Chief Marketing Officer) Metals and Minerals. Ave and Paramita have skills and industry perspectives that are highly relevant to our business.
With these changes, the Board of Directors consists of 10 members, nine of whom are independent.
Connecting from a new corporate headquarters
After some 50 years in the same location in Vaughan, Ontario, Toromont will construct a new headquarters ~10 km northwest of our existing facility on part of a parcel of land we acquired several years ago. With occupancy planned for 2027, this 190,000 sq.ft. facility will be shared with a Toromont Cat branch. It will be purpose built using mass timber construction and will leverage the capabilities of Toromont Power Systems and CIMCO to achieve energy efficiency. Beyond reducing our relative carbon footprint compared to our old headquarters, it will provide Toromont with the capacity to grow and better serve customers for decades to come. Substantial urban growth in the area surrounding our existing facility in Vaughan means that the eventual sale of that property for redevelopment should allow us to realize funds that will offset the cost of this move.
Connecting as a driven, disciplined and dedicated team
Disciplined fiscal management is vital for our business, which regularly encounters cyclicality in our customers’ capital investment cycles and changes in the economic environment. Ultimately, decision making on where, when and how much to spend and invest is dependent on experience, good judgement and sound business cases. While we act with a long-term mindset, our approach keeps us grounded in the day-to-day results of every Toromont branch so that we can understand customer requirements, what is working and what needs to be course corrected. It is here that accountability for the short and long term plays out in real time.
In 2025, our pledge to all stakeholders is to act responsibly and with balance, so that we can continue to connect Toromont with the best growth and performance opportunities now and in the future as a Driven, Disciplined and Dedicated team.
Yours sincerely,
Richard G. Roy
Chair of the Board of Directors
Mike S. H. McMillan
President and Chief Executive Officer